Our Blog
The Importance of Material Selection in RF Welding
Share this Article:
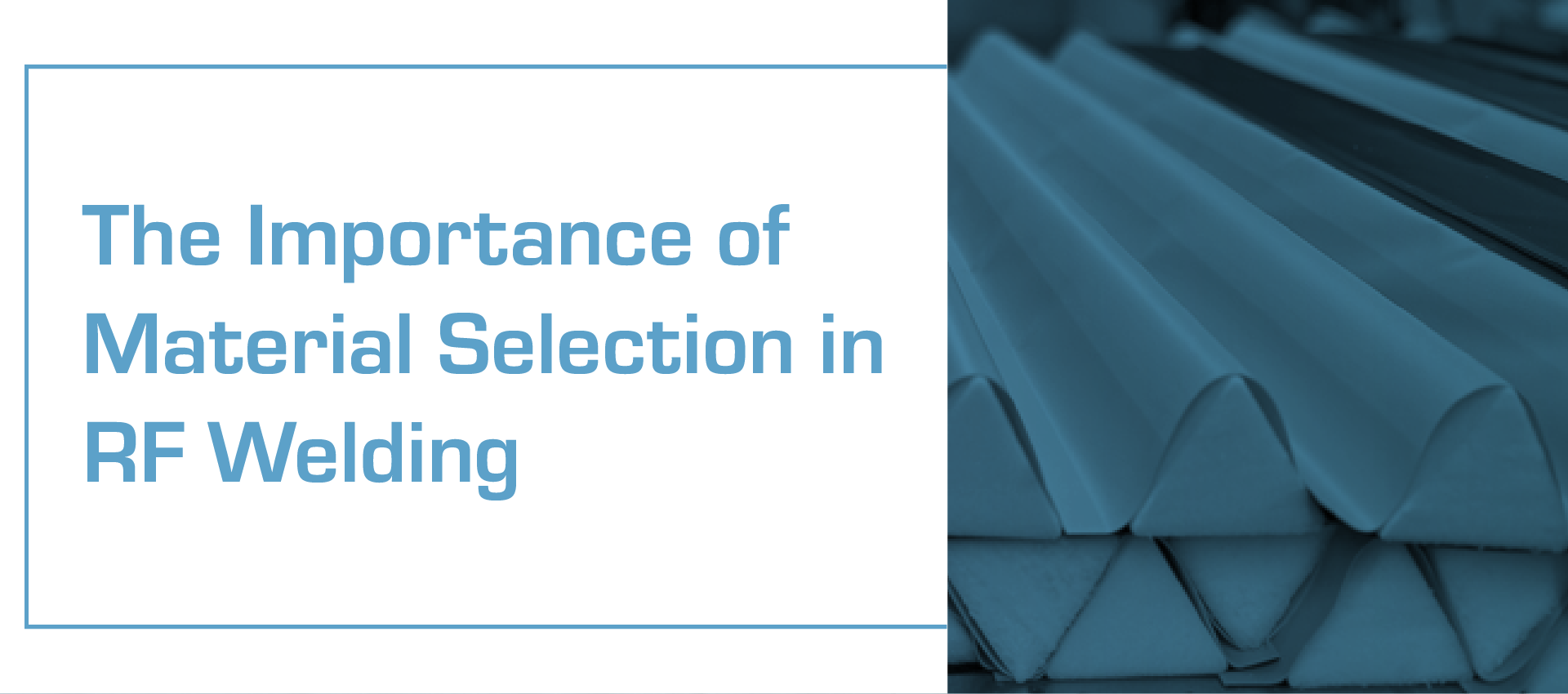
RF welding creates strong, sealed bonds in flexible materials using radio frequency energy. The material used plays a critical role in how effective the weld will be. Choosing the right one ensures durability, performance, and a reliable final product.
How Does RF Welding Work?
RF welding uses high-frequency electromagnetic energy to generate heat between layers of thermoplastic material. The energy excites the molecules within the material, causing them to heat up and fuse together under pressure. Once cooled, the materials form a solid, uniform bond without the need for stitching or adhesives.
This process is ideal for applications that require airtight or watertight seals, especially in products made from compatible flexible materials.
How Materials React to RF Welding
Not all materials respond the same way to RF welding. Materials with polar molecular structures, such as certain thermoplastics, absorb radio frequency energy effectively and form strong, consistent bonds. These materials heat evenly and weld well under pressure.
Non-polar materials resist this energy and typically do not weld successfully. Using incompatible materials can lead to weak seams, poor performance, or complete bond failure.
Understanding how a material behaves under RF energy is key to producing a reliable and durable product.
Best Materials for RF Welding
RF welding is most effective with polar thermoplastics. These materials respond well to radio frequency energy and produce strong, consistent bonds.
PVC (Polyvinyl Chloride)
PVC is one of the most commonly used materials in RF welding. It responds well to high-frequency energy, creating strong, airtight bonds. It’s available in a wide range of thicknesses, colors, and finishes, making it a versatile choice for many applications, including protective covers,
medical products, and fluid containment systems.
Polyurethane (PU)
Polyurethane is a flexible, durable material that welds well using RF energy. It offers excellent abrasion resistance and elasticity, making it a good option for products that need to stretch, flex, or withstand repeated use. PU is often used in inflatable structures, protective gear, and industrial bladders.
EVA (Ethylene Vinyl Acetate)
EVA is a soft, flexible material that performs well in RF welding. It bonds cleanly and holds up to wear, moisture, and environmental stress. EVA is often used in medical bags, flexible pouches, and soft enclosures where clarity and flexibility are important.
TPU (Thermoplastic Polyurethane)
TPU is known for its balance of flexibility and strength. It responds reliably to RF welding and maintains its shape under stress. Its toughness makes it a strong choice for applications that demand both elasticity and structural integrity, such as pressure bladders, reinforced seams, and rugged outdoor components.
Materials That Don’t Work Well with RF Welding
Some materials lack the molecular structure needed to absorb RF energy and cannot be welded using this process. Non-polar plastics like polyethylene (PE), polypropylene (PP), and most nylons do not react to RF energy and require alternative bonding methods such as heat sealing, adhesives, or mechanical fasteners.
Using incompatible materials in RF welding can result in weak seams or failed bonds, making it important to match the material to the process from the start.
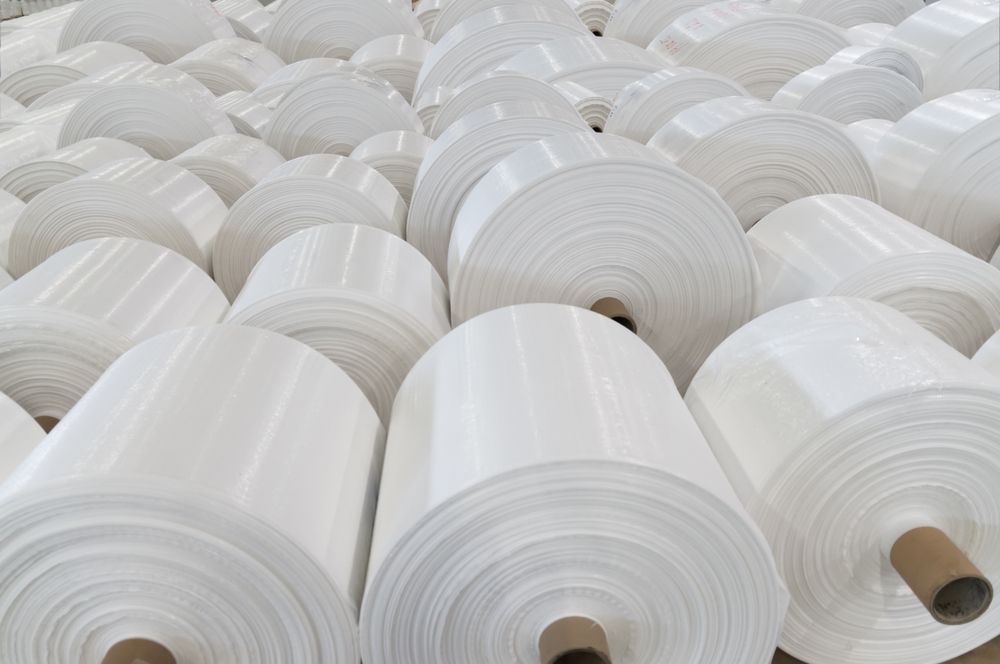
How Material Affects Final Product Performance
RF welding is most effective with polar thermoplastics. These materials respond well to radio frequency energy and produce strong, consistent bonds.The material used in RF welding directly influences how the final product performs. Strength, flexibility, resistance to wear, and ability to hold a seal all depend on the material’s properties. For example, a product exposed to UV light or chemicals will require a material that can withstand those conditions without breaking down.
Choosing the right material helps the product function as intended, meet safety or industry standards, and hold up under real-world use.
Common Use Cases Where Material Selection Makes a Difference
In RF welding, the right material can make or break a product’s performance in real-world conditions. Different industries face different challenges, and the material must align with those demands.
- Medical: Products like fluid bags, air bladders, or protective barriers must use materials that are clean, consistent, and safe for direct or indirect patient contact. Clarity, chemical resistance, and the ability to create leak-proof seals are often required.
- Industrial: Equipment covers, baffles, or liners may need to resist abrasion, chemicals, or fluctuating temperatures. Material thickness, strength, and weld integrity all play a role in protecting critical assets.
- Environmental: Applications like spill containment, water storage, and inflatable barriers must hold up to the elements. UV resistance, flexibility across temperature extremes, and long-term weld stability are essential.
- Outdoor and Specialty Gear: In tents, inflatables, and technical packs, material choice affects packability, weight, and field durability. A poor choice can lead to seam failures or early wear.
Across all of these uses, the welding process can only perform as well as the material allows. Matching the right material to the environment and performance goals is key to delivering a dependable product.
How Carolina CoverTech Helps You Choose the Right Material
Choosing the right material for RF welding isn’t just about compatibility. It’s about finding the best fit for the product’s purpose, environment, and performance requirements. Carolina CoverTech brings decades of experience in both material behavior and RF welding techniques to guide that decision.
Our team works closely with clients to understand the application, evaluate options, and recommend materials that weld reliably and hold up over time. From prototyping to full production, we help ensure your product is built with the right foundation from the start.
Have a project that calls for RF welded materials?
Contact us today to get expert guidance and support.