Our Blog
The Complete Guide to RF (Radio Frequency) Welding
Share this Article:
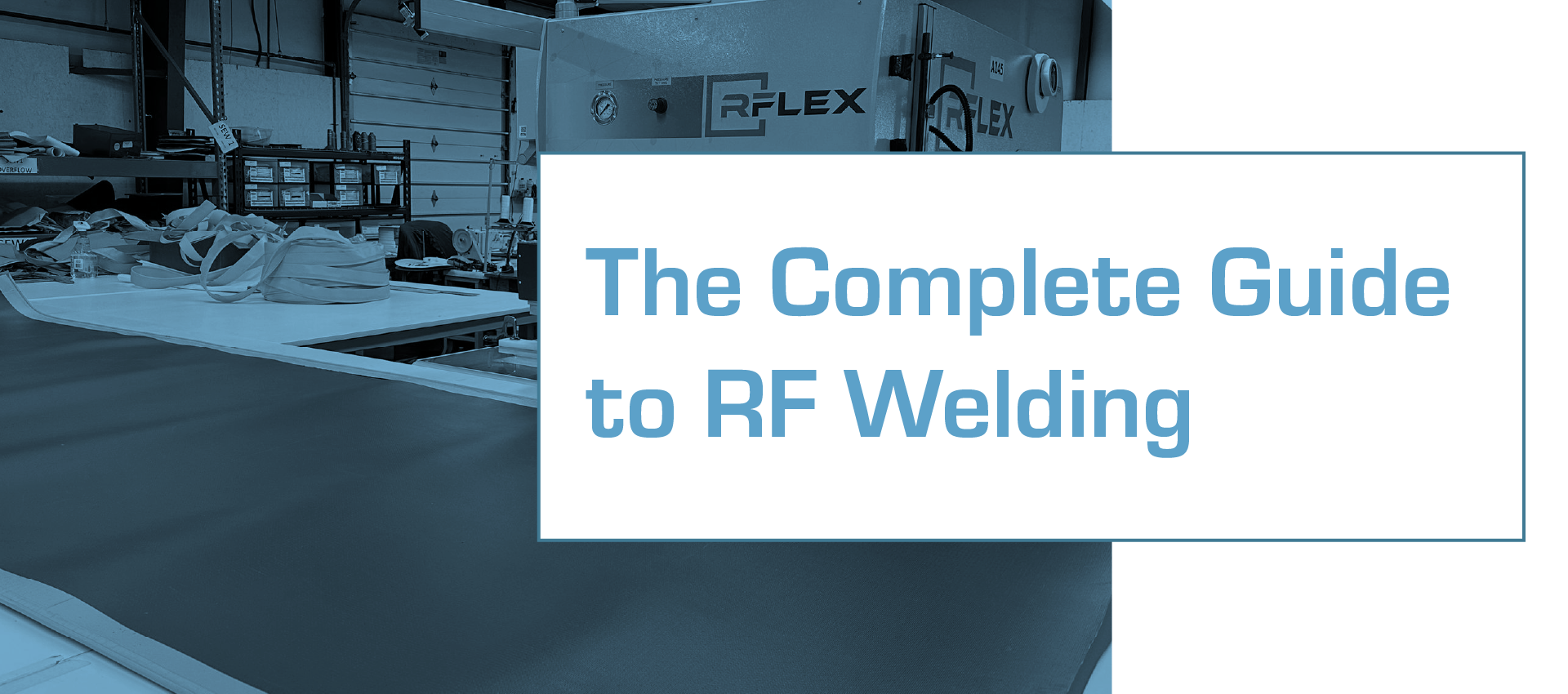
What is RF (Radio Frequency) Welding?
RF (Radio Frequency) welding, also known as high-frequency welding or dielectric sealing, is a process that uses electromagnetic energy to fuse materials together. This method is commonly used for thermoplastics and creates a strong, airtight, and watertight seal without the need for adhesives or stitching. Unlike traditional heat-based welding, RF welding generates heat internally within the material, ensuring a consistent and durable bond.
This process is widely used across various industries, including medical, industrial, military, and consumer applications, where airtight and waterproof seals are required.
How Does RF Welding Work?
RF welding works by applying high-frequency electromagnetic energy to two layers of thermoplastic material placed between two electrodes. The radio frequency waves cause the molecules within the materials to vibrate, generating heat from the inside out. This internal heating softens the plastic, allowing the layers to fuse together under applied pressure. Once the energy is turned off, the material cools and forms a permanent bond.
The key advantage of RF welding is its precision. Unlike traditional heat sealing, which relies on external heat sources, RF welding selectively heats only the bonding area, minimizing material distortion and resulting in a uniform seal.
When Was RF Welding Popularized?
RF welding emerged in the early 20th century but became widely used in the 1940s and 1950s. During World War II, advancements in radio frequency technology led to its application in bonding materials for military and industrial use. As the plastics industry grew, RF welding replaced stitching and adhesives in many applications, becoming a preferred method for creating durable, airtight seals.
Advancements in RF Welding
Over the years, RF welding has evolved with improvements in precision, efficiency, and material compatibility. Modern RF welding machines now feature advanced controls, allowing for better temperature regulation and more consistent welds. Innovations in electrode design and automation have also expanded the range of materials that can be welded, making the process even more versatile.
Recent advancements include computerized RF welding systems that enhance quality control and reduce waste. These improvements have made RF welding an even more reliable solution for industries requiring airtight, watertight, and durable seals.
What Equipment & Machinery is Needed for RF Welding?
RF welding requires specialized equipment designed to generate and control high-frequency electromagnetic energy. The main components include:
- RF Generator: Produces high-frequency energy to heat and fuse materials.
- Electrodes/Tooling: Custom-shaped electrodes apply pressure and direct energy to the bonding area.
- Press System: Holds materials in place and applies the necessary force for a strong seal.
- Cooling System: Ensures proper material cooling to solidify the bond.
Modern RF welding machines vary in size and complexity, from manual presses for small-scale operations to fully automated systems for high-volume production. The choice of equipment depends on the material, product design, and production requirements.
Benefits of RF Welding vs. Other Types of Welding
RF welding offers several advantages over other welding methods, particularly when working with flexible thermoplastics. Some key benefits include:
- Stronger, Airtight Seals: RF welding creates uniform bonds that are airtight, watertight, and highly resilient.
- Precise, Controlled Heat Application: Unlike traditional heat sealing, RF welding generates heat internally, reducing material distortion and improving consistency.
- No Need for Adhesives or Additional Fasteners: This eliminates the risk of chemical breakdown over time and results in a cleaner, more efficient bonding process.
- Faster Processing Times: RF welding is highly efficient, producing strong seals in seconds and accelerating production speed.
While other welding methods like ultrasonic welding or hot air welding have their advantages, RF welding is ideal for applications that require flexibility, strength, and resistance to environmental conditions.
Potential Drawbacks of RF Welding
While RF welding offers many advantages, it does have some limitations, particularly when compared to other sealing methods like heat sealing. Some potential drawbacks include:
- Material Restrictions: RF welding is only effective with thermoplastics that have polar molecules, such as PVC and polyurethane. Materials like polyethylene and polypropylene require alternative welding methods.
- Equipment Costs: The specialized machinery for RF welding can be more expensive upfront than other sealing technologies.
- Limited to Certain Applications: RF welding works best for thin, flexible materials. For thicker or rigid materials, other welding techniques may be more suitable.
This is where heat sealing comes into play. Heat sealing, which uses direct external heat to bond materials, can be a more suitable option for non-polar plastics or applications that don’t require the precision of RF welding. Manufacturers often assess the material, production volume, and sealing requirements to determine the best method for each project.
What Types of Materials Are Best Suited for RF Welding?
Certain thermoplastics are particularly well-suited for RF welding due to their polar molecular structure, which allows them to respond effectively to high-frequency energy. The most commonly used materials include:
- Polyvinyl Chloride (PVC): One of the most widely used materials for RF welding due to its flexibility, strength, and excellent sealing properties.
- Polyurethane (PU): Offers similar benefits to PVC but with greater elasticity and chemical resistance, making it ideal for medical and industrial applications.
- Nylon (in some cases): Certain nylon formulations can be RF welded, especially when coated with a compatible thermoplastic layer.
What Types of Products Need RF Welding?
Many products require strong, airtight, and watertight seals that RF welding can provide. This method is commonly used for:
- Medical Devices & Equipment: IV bags, blood pressure cuffs, and fluid containment systems rely on RF welding for sterile, leak-proof seals.
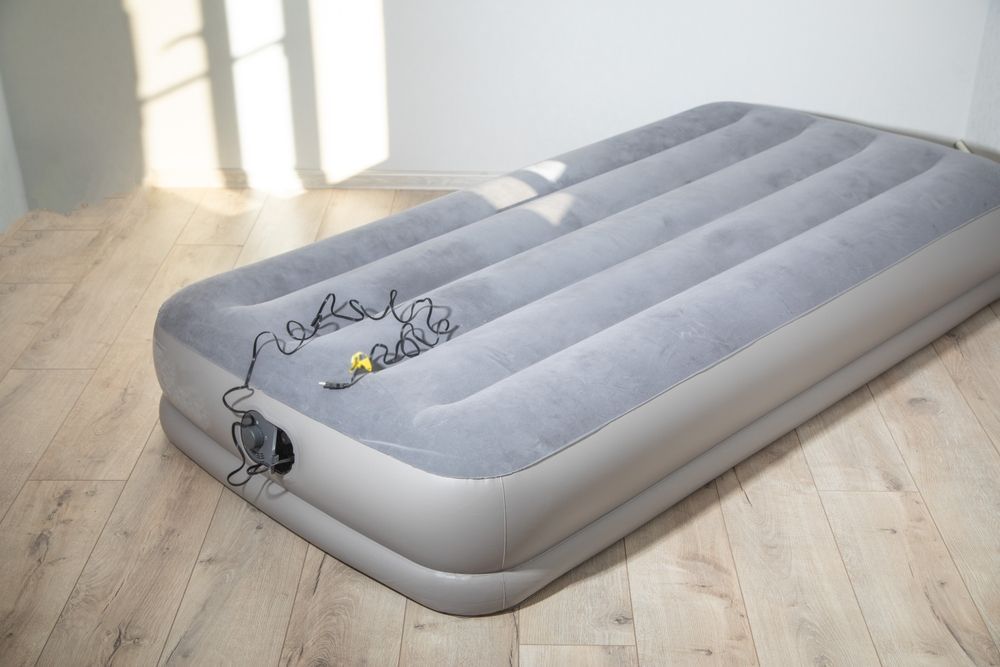
- Inflatable Products: Air mattresses, life vests, and medical air cushions need airtight bonds to maintain functionality.
- Protective Covers & Enclosures: Industrial tarps, protective cases, and weather-resistant enclosures use RF welding for enhanced durability.
- Fluid & Chemical Containment: Bladders, tanks, and spill containment systems require precision sealing to prevent leaks and contamination.
The ability to create seamless, high-quality seals makes RF welding an essential process for products used in demanding environments.
Common Industry Applications of RF Welding
A wide range of industries rely on RF welding to produce high-quality, durable products. Some of the most common sectors utilizing this technology include:
- Medical & Healthcare: RF welding is essential for manufacturing sterile medical bags, surgical covers, and inflatable cushions used in patient care.
- Aerospace & Defense: The military and aerospace industries use RF welding for protective gear, fuel bladders, and inflatable structures that require airtight seals.
- Industrial & Manufacturing: Custom protective covers, containment solutions, and flexible storage tanks benefit from RF welding’s strength and reliability.
- Outdoor & Recreation: Inflatable boats, life jackets, and waterproof gear require precision sealing to maintain their durability in harsh conditions.
Because RF welding creates strong, flexible, and watertight seals, it is the preferred choice for industries that demand high performance and longevity.
Who is Capable of RF Welding?
Not all manufacturers have the expertise or equipment to perform RF welding. This process requires specialized machinery, precise tooling, and skilled technicians to ensure strong, consistent welds. Companies that specialize in RF welding typically have:
- Advanced RF Welding Equipment: Precision machinery designed to handle various materials and product specifications.
- Experienced Engineering Teams: Experts who understand material compatibility, tooling design, and production efficiency.
- Quality Control Processes: Rigorous testing and inspection to guarantee airtight, watertight, and long-lasting seals.
At Carolina CoverTech, we have decades of experience in RF welding and the capabilities to handle complex projects with precision and efficiency. Our team works closely with partners to develop and manufacture high-quality products that meet the toughest industry demands.
Carolina CoverTech Can Take Care of Your RF Welding Needs!
When it comes to RF welding, expertise, and precision matter. At Carolina CoverTech, we specialize in creating strong, airtight, and watertight seals for a wide range of industries. With years of experience, advanced RF welding technology, and a commitment to quality, we help businesses develop and manufacture products that cover, protect, contain, and enclose.
Whether you need medical-grade containment solutions, industrial protective covers, or custom-sealed products, our team is ready to bring your vision to life. Contact us today to discuss your RF welding needs and discover how we can be your trusted manufacturing partner!